Introducing: The art of filigree
Filigree is a traditional jewelry-making technique known for its delicate craftsmanship. It involves twisting ultra-fine gold or silver wires in pairs, flattening them, and carefully arranging them onto a pre-made framework, also in gold or silver, to create intricate designs.
Portuguese Filigree traditional patterns
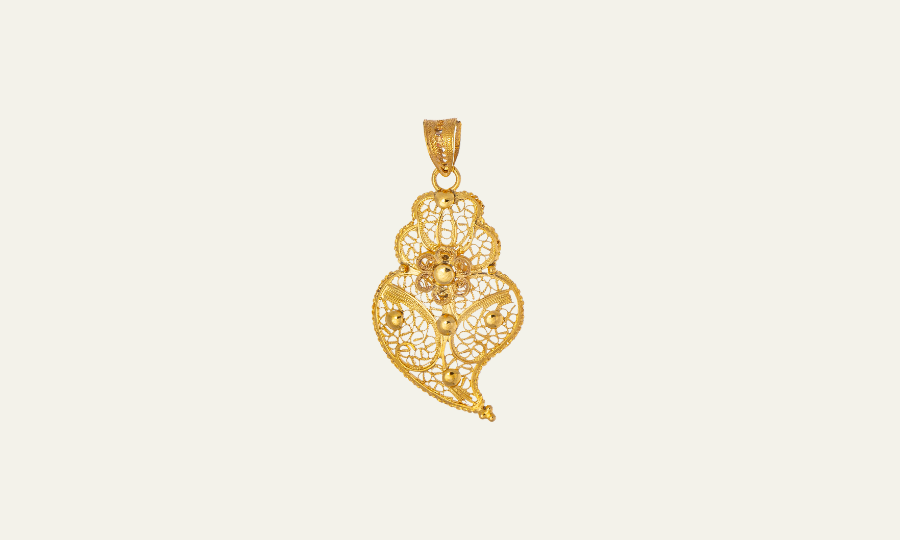
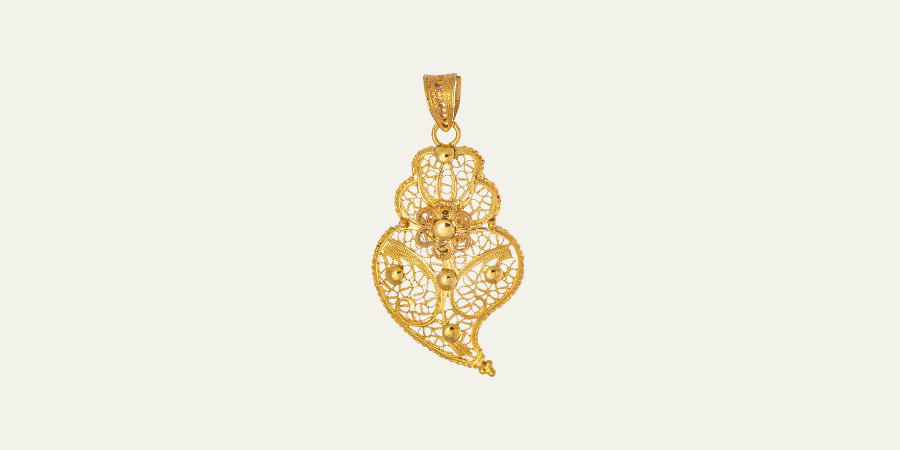
Viana Heart
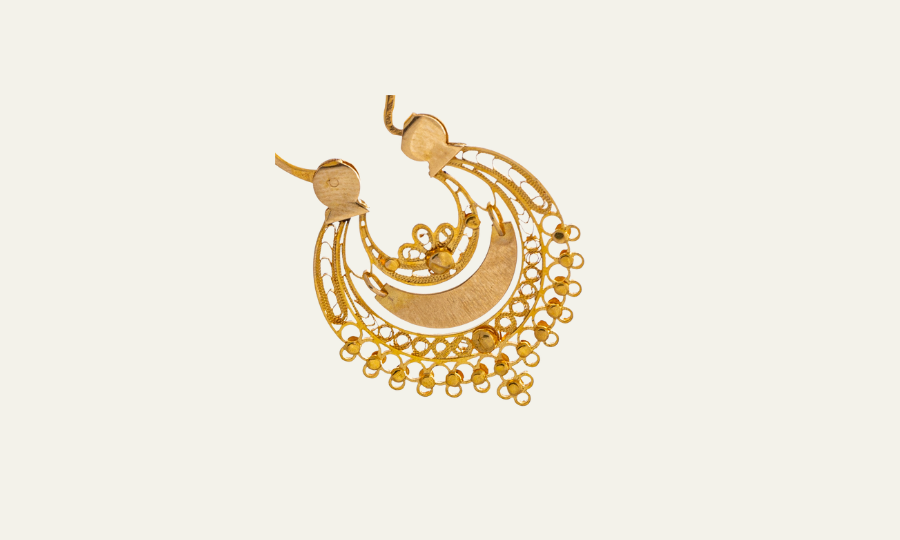
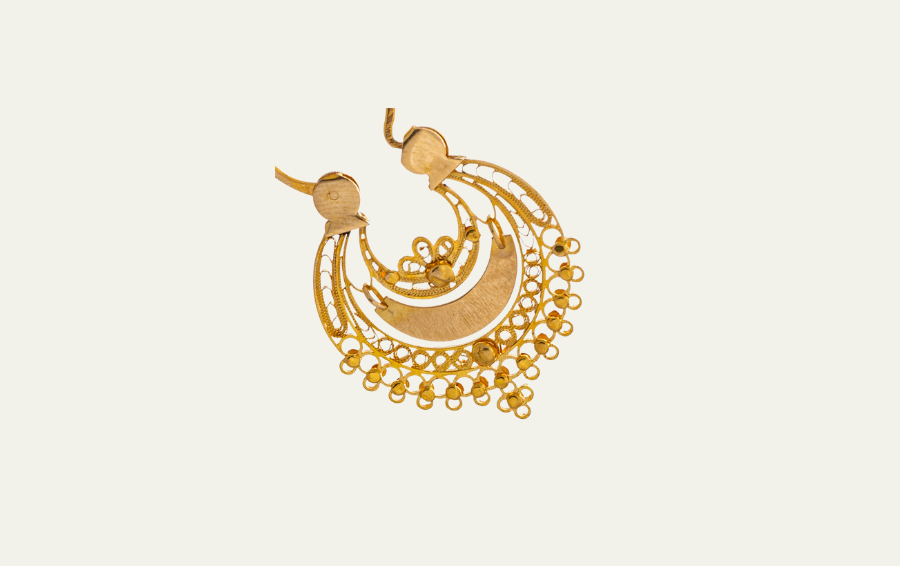
Arrecadas Earrings
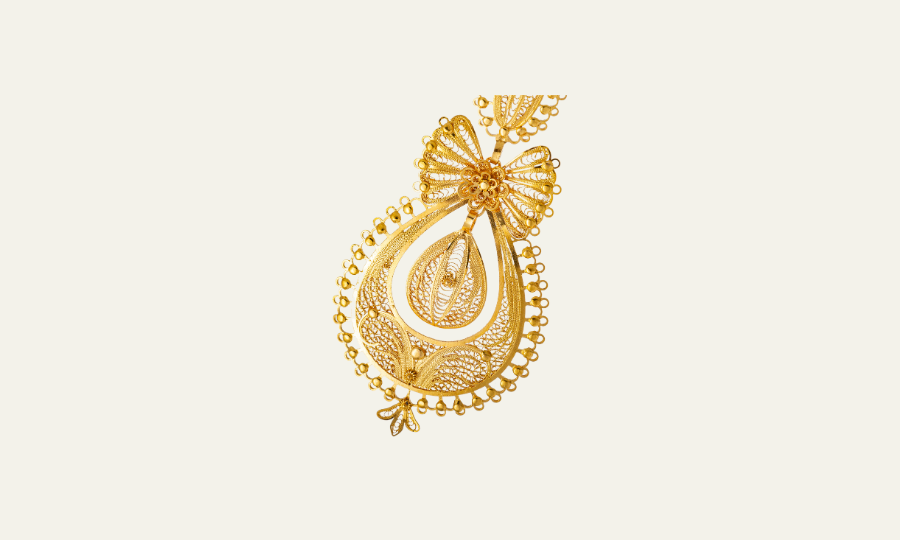
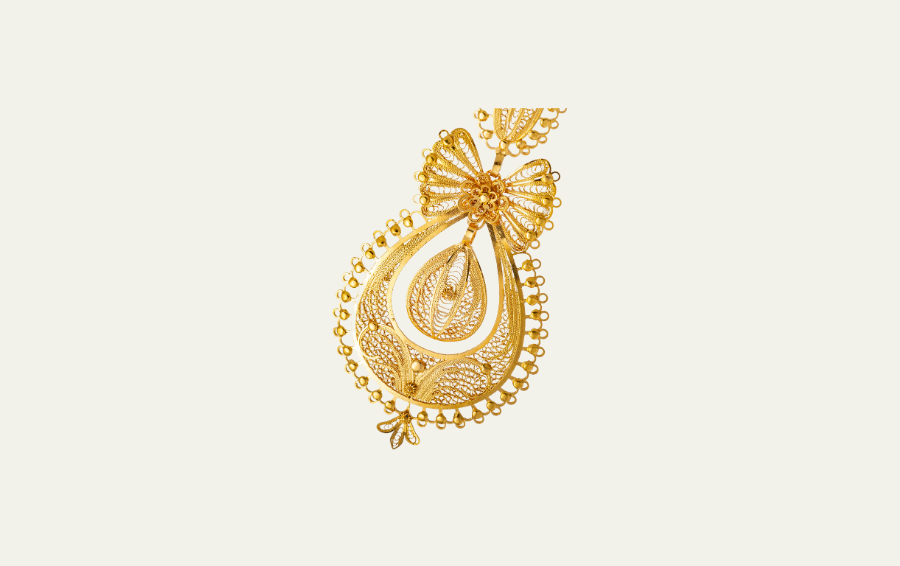
Princess Earrings
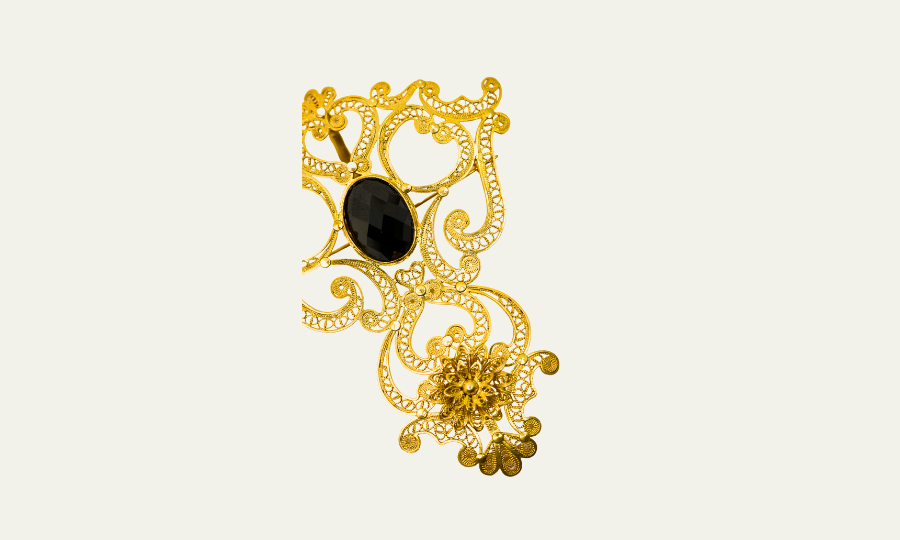
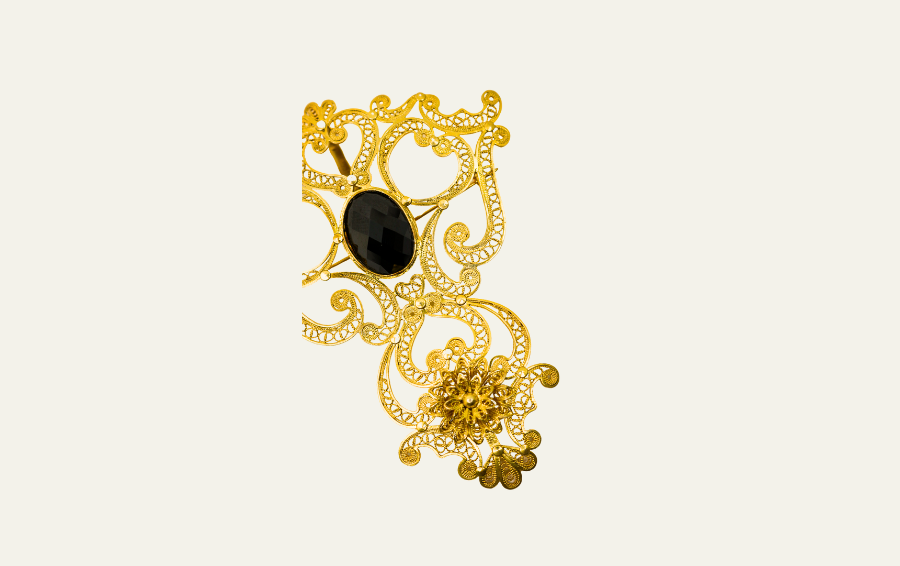
Laça
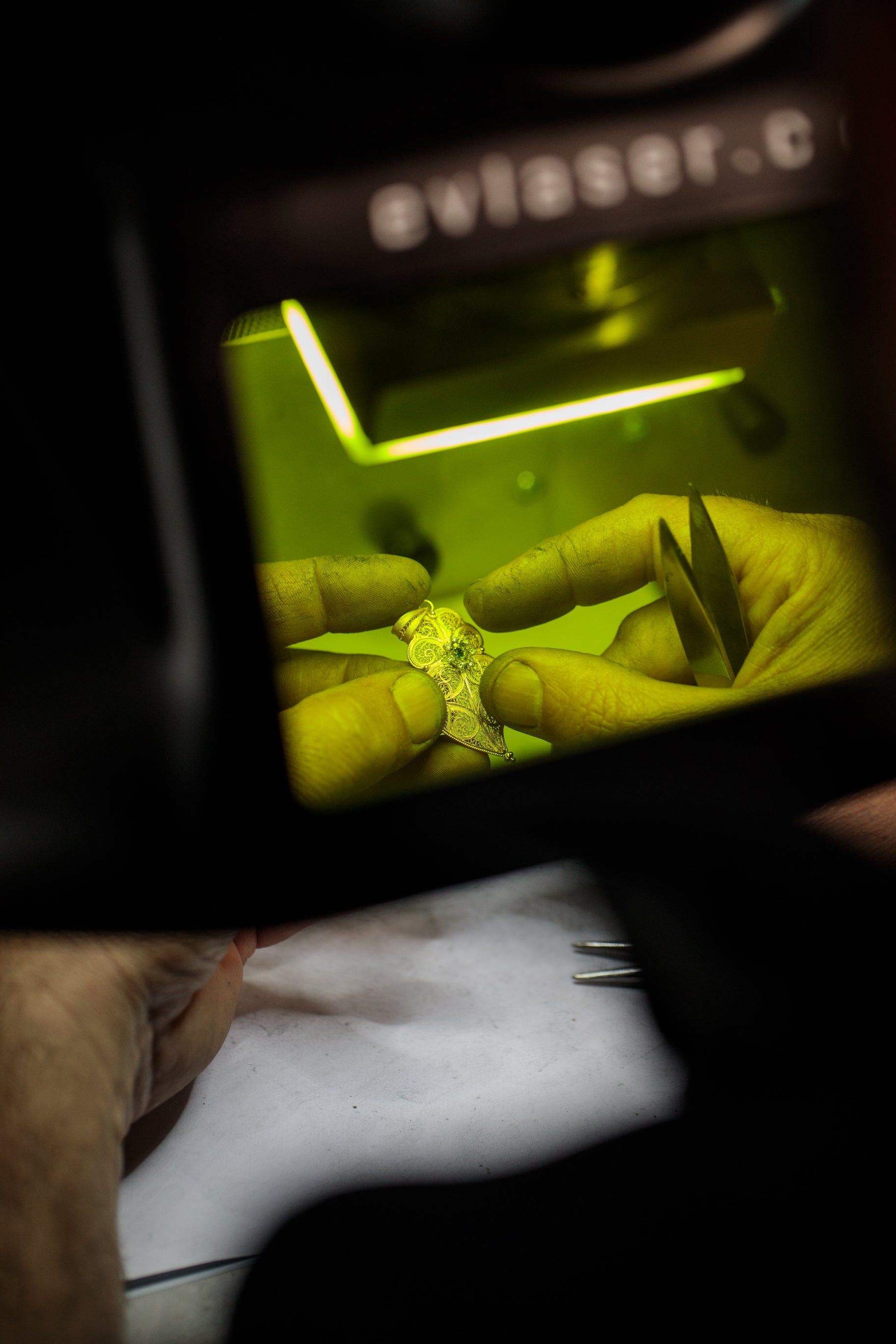
Carmo's Commitment to Innovation
A new wave of artisans—many trained in design, jewelry making, and traditional filigree techniques—are bringing fresh creativity to Portuguese filigree. This craft now thrives through artisans who blend technical mastery with artistic vision, redefining tradition without losing its soul.
Even abstract or unconventional shapes can earn official certification, as long as they preserve the essence of filigree’s techniques and Portuguese heritage.
Joalharia do Carmo proudly supports this new generation of designers and artisans, contributing to the evolution of this timeless art form. In this spirit, we offer our own exclusive collection of jewelry pieces—crafted with innovative shapes and designs that honor the tradition of filigree while embracing its exciting future.